L’organizzazione dei siti di stoccaggio ricopre un ruolo di grande importanza all’interno dei processi di logistica, specie se le merci depositate in magazzino sono destinate ad essere movimentate di frequente per essere destinate alla vendita o ad altri siti di lavorazione. In tal caso, la fase di picking assume una funzione essenziale e, di conseguenza, va predisposta e gestita in modo tale da ottimizzare l’intero processo, così da renderlo più efficace e ridurre gli sprechi di tempo. In questo articolo vedremo come implementare la gestione dell’area picking per massimizzare l’efficienza logistica della gestione delle risorse di magazzino.
Leggi anche cosa vuol dire Stoccaggio e come si effettua.
Cosa sono le aree di picking in magazzino
All’interno di un magazzino (o di un sito di stoccaggio analogo), le aree di picking sono le zone deputate esclusivamente alla selezione e al prelievo della merce in deposito, sia si tratti di singoli oggetti sia di imballaggi o fardelli preconfezionati. Le operazioni di picking possono essere effettuate manualmente da un operatore oppure per mezzo di sistemi di automazione, a seconda delle dimensioni e dell’organizzazione interna del magazzino. In ogni caso, l’area destinata al picking deve essere organizzata in maniera razionale e funzionale, per agevolare le operazioni di prelievo e successiva movimentazione.
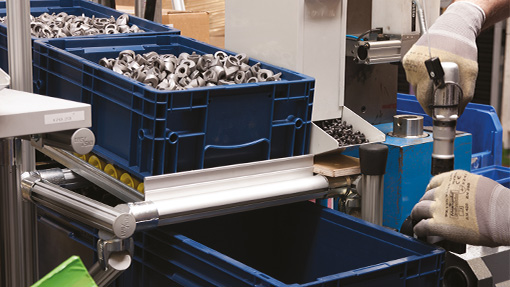
Area di picking in magazzino
Come e dove si allestiscono
Il fattore principale da prendere in considerazione quando si progetta l’allestimento di un’area di picking è il posizionamento. La scelta dipende essenzialmente dai seguenti fattori:
- Dimensioni del locale di stoccaggio;
- Flusso di materiale o articoli gestito quotidianamente all’interno del magazzino;
- Organizzazione e livello di automazione del sito.
Dalle dimensioni della struttura di deposito dipendono alcune prerogative che influiscono in maniera significativa sulla gestione delle aree di picking, ossia la modalità di prelievo e l’estensione delle scaffalature. In un magazzino dalle dimensioni contenute, è probabile che il prelievo venga effettuato manualmente dagli operatori preposti; di conseguenza, il livello di automazione potrebbe essere molto basso (o addirittura nullo). Ciò non toglie che l’area deputata al prelievo vada organizzata in maniera tale da ottimizzare le procedure di picking, scegliendo una collocazione adeguata; nel caso in cui si tratti di un magazzino in cui sono stoccati gli articoli di un negozio al dettaglio, la collocazione ideale dell’area di prelievo è in una zona in prossimità del punto vendita.
I siti di stoccaggio più grandi, che gestiscono quotidianamente grandi flussi di articoli in entrata e in uscita ricorrono a sistemi più o meno estesi di automazione, variando la collocazione dell’area di picking a seconda di specifiche esigenze logistiche. In tal senso, le opzioni più diffuse per la dislocazione delle aree di picking sono due:
- Presso la testata del magazzino; questa soluzione è particolarmente adatta ai magazzini automatizzati di grandi dimensioni all’interno dei quali vengono gestite ingenti quantità di materiale. La testata, ossia l’area che fa da ponte tra l’interno e l’esterno del sito di stoccaggio, quando ospita l’area di picking funge anche da polo di smistamento per le spedizioni;
- Al centro o lungo un lato; entrambe le soluzioni non vengono adottate in maniera estemporanea ma scaturiscono da precise scelte di progettazione degli spazi, congruente con un layout specifico, elaborato per ottimizzare i processi di gestione dei flussi in entrata e in uscita. In contesti di questo genere, si rende necessario un grado di automazione superiore, da ottenere per mezzo di appositi apparati, come ad esempio i nastri trasportatori o i trasloelevatori. In aggiunta possono rendersi necessarie specifiche sovrastrutture, se il sito di stoccaggio si sviluppa su più piani o prevede scaffalature che si sviluppano in altezza.
Come organizzare e ottimizzare un’area di picking
L’organizzazione logistica di un’area di picking interviene su ogni fattore in grado di incidere sul processo di prelievo:
- La gestione degli spazi di stoccaggio;
- I sistemi di supporto all’intervento umano e per l’automazione del magazzino;
- Le modalità di stoccaggio.
Lo scopo funzionale della gestione delle aree di selezione e picking, come già evidenziato in precedenza, è l’ottimizzazione; in altre parole, un’organizzazione razionale e oculata persegue obiettivi ben precisi, ossia facilitare la selezione e il prelievo degli oggetti e dei materiali dal punto di stoccaggio, accelerare i tempi di movimentazione e adeguare le modalità di picking al volume di articoli e oggetti coinvolti quotidianamente nella lavorazione. Dal punto di vista pratico, questi obiettivi possono essere raggiunti adottando svariate soluzioni, anche molto diverse tra loro, purché in grado di rispondere alle necessità logistiche del sito di stoccaggio.
Per le strutture particolarmente ampie, i sistemi di automazione sono la soluzione ottimale; naturalmente, esistono diversi gradi di meccanizzazione, che vanno da un livello base ad una gestione completa del magazzino attraverso appositi software e dispositivi meccanici. Il modello organizzativo del sito di stoccaggio impone una precisa scelta in termini di gestione del rifornimento dell’area picking, secondo pattern diversificati individuati in risposta alle specifiche esigenze di movimentazione.
Ottimizzare l’area imparando a sfruttare i contenitori
C’è anche un altro elemento in grado di contribuire positivamente all’organizzazione delle aree di prelievo all’interno dei magazzini: si tratta dei contenitori, ossia i dispositivi rigidi all’interno dei quali vengono sistemati gli articoli o i fardelli da prelevare e trasferire. La scelta di un contenitore va effettuata in maniera ponderata, poiché può rappresentare un ulteriore fattore di ottimizzazione del processo di picking. Ogni dispositivo utilizzato deve adattarsi alle caratteristiche di ciò che conterrà e, al contempo, essere in grado di supportare sistema integrati di gestione automatizzata.
Per i materiali di piccole e medie dimensioni (genericamente indicati come “minuteria”) è consigliabile optare per scatole o box rigidi ‘su misura’, come le cassette portaminuteria in plastica Zeus di iMilani. Queste cassette rappresentano una soluzione pratica e versatile, in quanto sono impilabili e leggere, nonché facili da pulire. In alternativa, è possibile impiegare un altro genere di dispositivo, simile per funzionalità ma dalle prerogative differenti: i contenitori a bocca di lupo Compat. A differenza delle scatole standard, sono caratterizzare da un’apertura più pronunciata sulla parete frontale, che assicura una maggiore visibilità del contenuto interno. Inoltre, offrono le stesse prerogative delle altre cassette, in quanto sono facilmente impilabili e comode da maneggiare, oltre ad offrire una buona resistenza meccanica grazie ai rinforzi laterali.
Contenitori portaminuteria iMilani